This paper introduces a kind of environmental protection
quartz sand pickling treatment method.
In recent years, high-purity quartz sand has been gradually introduced into laser, semiconductor, microelectronics and other high-tech industries. Due to the impurities such as iron, aluminum, phosphorus, titanium, potassium and calcium adhering to the surface layer of the newly mined quartz, the purity and quality of the product are seriously affected, so the impurity removal process of quartz is the key part of the quartz sand production process. The purification of quartz sand to a higher purity requires a series of complex separation processes. However, the magnetic separation process often can not completely remove the iron-bearing mineral impurities in quartz sand, but also requires acid pickling to further remove the film iron wrapped on the surface of quartz sand particles. Acid leaching can also remove the carbonate impurities associated with quartz sand to further purify quartz sand. In the process of preparing quartz sand, the prior art usually needs acid pickling to remove iron and other impurities. If the waste acid after pickling is discharged directly, it will cause serious environmental pollution and is not conducive to cost saving. At the same time, the existing acid used in the preparation of quartz sand is a mixture of various acids, which is troublesome to prepare; the pickling process is complex and the iron content of the final quartz sand product is high.
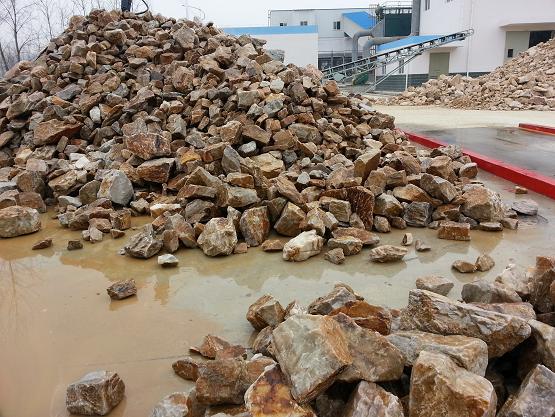
Sinonine provides a kind of environmental protection quartz sand pickling treatment method. On the premise of ensuring good purification effect of quartz sand, the waste acid produced in pickling process is recycled. And the by-products produced by the pickling cycle process are reused.
This quartz sand pickling technical scheme is realized by the following steps:
1. Acid leaching: put the quartz sand of appropriate particle size obtained through the previous process into the acid leaching tank, add hydrochloric acid, and carry out acid leaching to remove iron. The concentration of hydrochloric acid is 18%, the mass ratio of quartz sand to hydrochloric acid is 1:0.3-0.5, and then heated to 50-70 ℃ for 2-3 hours.
2.The first centrifugation: the quartz sand after acid leaching in step 1 is centrifuged to separate the sand and acid. The separated hydrochloric acid is returned to the acid leaching tank in step 1 for reuse. At the same time, the quartz sand containing part of hydrochloric acid after centrifugation is sealed and oxidized.
3. Sealed oxidation: add H2O2 with strong oxidation effect to the acid leaching tank, seal and oxidize it, and then clean it after oxidation. The cleaned quartz sand material enters the neutralization tank. Add 9% H2O2, 5-10% of quartz sand, heat 70-85 ℃, and seal and oxidize for 4-8 hours.
4.Neutralization: put alkaline substance into neutralization tank to neutralize quartz sand containing part of hydrochloric acid. After reaction for a certain period of time, quartz sand at the bottom of sedimentation tank and salt solution at the top of tank can be obtained. The basic material is calcium hydroxide, the amount of calcium hydroxide is 5-10% of quartz sand, and the neutralization time is 2-5 hours.
5. The first cleaning: use the salt solution on the upper part of the neutralization tank to clean the quartz sand in the tank for the first time.
6. The second centrifugation: the quartz sand after the first cleaning is put into the centrifuge for the second centrifugation, and the quartz sand obtained after centrifugation is cleaned for the second time by the past ionic water, and dried after cleaning, which is the finished product; the calcium chloride obtained after centrifugation enters the replacement tank.
7. Replacement: after calcium chloride enters into the replacement tank, sulfuric acid is added to the replacement tank to make it undergo replacement reaction to generate hydrochloric acid and calcium sulfate. The generated hydrochloric acid is returned to the acid leaching tank in step I for reuse. The by-product of calcium sulfate can be used as an additive for cement production. The amount of sulfuric acid added to the replacement tank is 10-30% of the amount of calcium chloride solution, and the replacement reaction time is 2-6 hours.
In this pickling process, the oxidation process is set up after the acid leaching and the first centrifugation. The quartz sand material after the acid leaching is sealed and oxidized by hydrogen peroxide. The purpose is to dissolve and separate the disseminated iron and iron-bearing minerals on the surface of quartz sand particles by oxidation, especially after the oxidation of divalent iron to trivalent iron, it is easier to remove iron by centrifugal cleaning.
The quartz sand pickling process has the following advantages:
1.Hydrochloric acid has been recycled. The waste hydrochloric acid obtained after the first centrifugation and the hydrochloric acid generated after the replacement in the replacement tank are all returned to the acid leaching tank for reuse. No waste acid is discharged directly into the environment, which not only completely solves the environmental pollution caused by the pickling link of the traditional purification method, but also reduces the production cost.
2.In the replacement process, through the replacement reaction of calcium chloride and sulfuric acid, calcium chloride is replaced into two useful by-products, namely hydrochloric acid and calcium sulfate. Hydrochloric acid is recycled in the process again. Calcium sulfate can be used as an additive for cement production and increase economic benefits for enterprises.
3.The process is simple, the design is reasonable, the waste of the whole production process is discharged, the production environment is improved, energy conservation and environmental protection are realized.
Remarks:Sinonine can provide all the technical support for the above pickling process, and can contact specific matters by email: [email protected].